Alcast Company Things To Know Before You Buy
Alcast Company Things To Know Before You Buy
Blog Article
The Best Guide To Alcast Company
Table of ContentsThe Alcast Company PDFs8 Easy Facts About Alcast Company ExplainedHow Alcast Company can Save You Time, Stress, and Money.Alcast Company - QuestionsExamine This Report about Alcast CompanyAlcast Company - QuestionsExamine This Report on Alcast Company

If you assume that a functioned alloy may be the best for your job, have a look at several of our articles that discuss more regarding details functioned alloys, such as Alloy 6061 and Alloy 6063. On the other hand, if you think a cast alloy would be better for you, you can discover more regarding some actors alloys in our Alloy 380 and Alloy 383 posts (coming quickly).
The Single Strategy To Use For Alcast Company
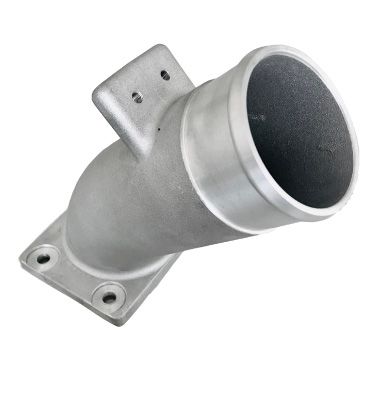
Having the experience and industry knowledge to engineer your castings for optimal production and quality outcomes will improve the project. Producing aluminum spreading calls for a facility set of processes to accomplish the best results. When making a decision on a brand-new aluminum foundry to partner with, guarantee they have considerable sector experience and are educated concerning all facets of the light weight aluminum casting process: layout, manufacturing, product analysis, and product screening.
(https://www.bark.com/en/us/company/alcast-company/p3P2O8/)The shop ought to additionally have a tested performance history of providing remarkable items that meet or surpass customer expectations. Quality assurance ought to additionally be at the top of your listing when picking an aluminum factory. By functioning with a qualified factory that follows the requirements for top quality control, you can protect the stability of your item and ensure it satisfies your requirements.
The Only Guide for Alcast Company
By selecting a firm that uses solutions that satisfy or exceed your product needs, you can be certain that your job will be completed with miraculous accuracy and performance. Specific aluminum foundries concentrate on details kinds of producing processes or casting approaches. Various parts require various production techniques to cast light weight aluminum, such as sand spreading or pass away casting.
Die casting is the name provided to the procedure of producing intricate metal parts through use of mold and mildews of the component, additionally known as dies. It generates more elements than any kind of other procedure, with a high level of accuracy and repeatability. There are 3 sub-processes that drop under the category of die casting: gravity pass away spreading (or permanent mold and mildew spreading), low-pressure die casting and high-pressure die casting.
After the purity of the alloy is evaluated, dies are produced. To prepare the passes away for spreading, it is important that the dies are clean, so that no residue from previous productions stay.
The pure steel, additionally called ingot, is included in the furnace and kept at the molten temperature of the metal, which is then transferred to the injection chamber and injected right into the die (Casting Foundry). The pressure is after that maintained as the steel strengthens. As soon as the metal strengthens, the cooling procedure starts
Top Guidelines Of Alcast Company
The thicker the wall surface of the part, the longer the cooling time due to the quantity of indoor steel that also requires to cool down. After the component is totally cooled, the die halves open and an ejection mechanism presses the component out. Following the ejection, the die is closed for the next injection cycle.
The flash is the extra product that is cast during the procedure. Deburring eliminates the smaller items, called burrs, after the trimming process.
All About Alcast Company
This proved to be an imprecise examination, due to the fact that the tester could cut right into a piece and miss out on a location with porosity. Today, leading makers utilize x-ray testing to see the whole interior of components without cutting right into them. This enables them to more accurately accept or decline parts. To obtain to the finished product, there are three main alloys utilized as die spreading material to select from: zinc, light weight aluminum and magnesium.
Zinc is one of one of the most used alloys for die casting due to its reduced expense of raw materials. It's also among the more powerful and steady metals. Plus, it has superb electrical and thermal conductivity. Its rust resistance also permits the elements to be long lasting, and it is just one of the much more castable alloys because of its lower melting point.
Alcast Company Can Be Fun For Everyone
As mentioned, this alloy is just one of the most typically used, yet makes will, at times, choose light weight aluminum over zinc due to light weight aluminum's production benefits. Aluminum is highly cost-effective and among the extra visit this website flexible alloys. Light weight aluminum is utilized for a number of different products and markets anything from window frames to aerospace products.
Report this page